金属加工液必须知道的六大问题
其一 水基切削液的质量控制项目有哪些?
水基切削液在应用时都是加水稀释的,其试验项目也可分为直接测定和加水测定两部分。直接测定的项目有存储安定性、硫及氯含量、不挥发组分等。加水后再测定的项目有表面张力、PH值、起泡性、防锈性、腐蚀性、抗菌性等。
其二 油基切削液与水基切削液各有什么特点? 总体来说,油基切削液的润滑性较好,而水基切削液的冷却性较好。油基切削液在高温时易产生烟雾、易着火;水基切削液易生菌腐败,使用期短,容易生锈。
其三 切削油的质量检测有哪些项目?
切削油的主要质量控制指标有粘度、闪点、倾点、脂肪含量、硫含量、氯含量、铜片腐蚀、水分、机械杂质、四球实验等。关于测定方法可参考试验方法标准。
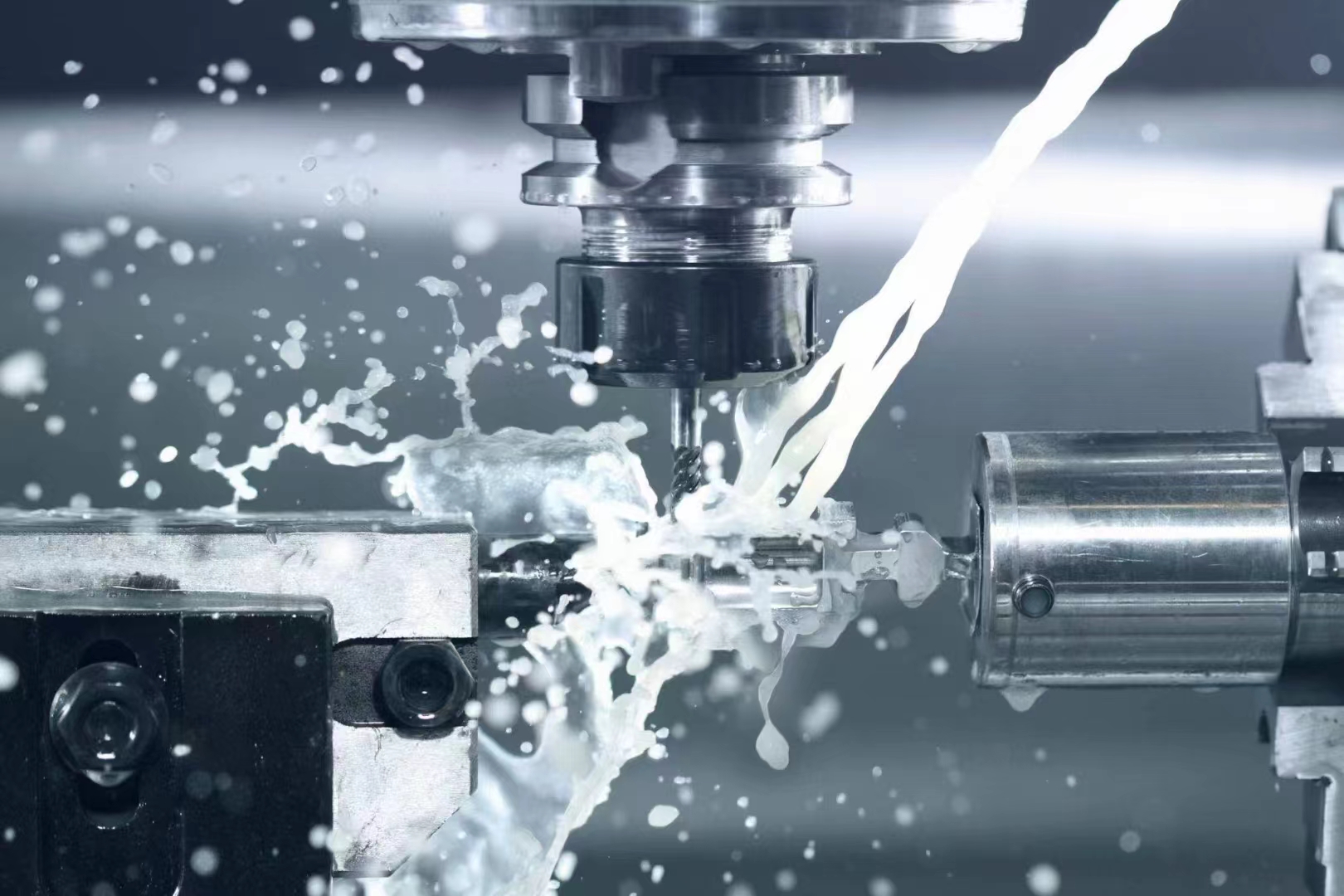
其四 选用切削液时要考虑哪些因素?
影响切削液选用的因素很多,有时一些看起来不太重要的因素却成了决定选型的关键。
例如插齿一般是粗加工,齿轮经插齿成型后尚需经剃齿工序进行精加工,选用活性低的切削油既可满足工艺要求,又可获得较长的刀具寿命。这一般是指在齿轮加工车间而言,若同一台插齿机是在一个修配车间里,齿轮加工的批量很小又无后续的剃齿工序,显然就应该选用高活性的切削油,因为此时产品的质量是主要因素,而刀具寿命及加工效率则是次要的。所以切削液的选用因素和步骤不是固定的。
一般情况而言,影响切削液的选用因素有加工方法、工件材料、刀具、加工参数、对加工产品的质量要求、职业安全卫生、废液处理、有关法规方面的规定等。
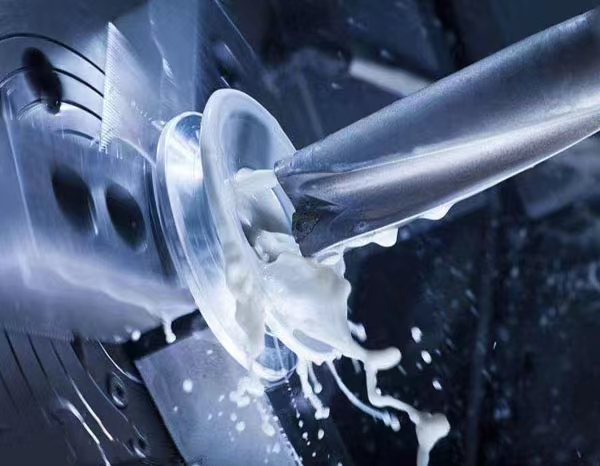
其五: 润滑性好的切削液是否就是高品质的?
这是一个被广泛误解的问题,有些人认为提高切削液的品质就是不断提高切削液的极压和润滑性,并企图用润滑性来划分切削液的质量档次。其实切削液的性能要求是多方面的,其所应具备的性能是根据实际应用的需要决定的。润滑性只是切削液的诸多功能之一,并非润滑性越高越好,过度的润滑往往会带来反作用,如因极压性过头产生了化学磨损,则会大大缩短刀具寿命,极压剂的应用会促进生锈和造成严重腐蚀,由于润滑性添加剂与工件表面形成的吸附膜,则会给工件的后处理及应用(如原子能工业及电子工业中的一些金属零件)带来麻烦。
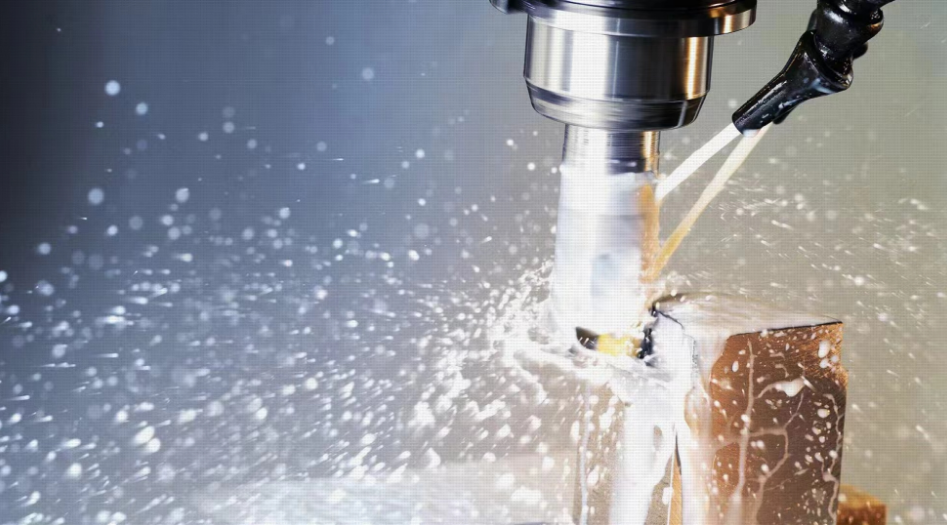
其六: 应如何正确看待切削液的作用及效果? 首先应该明确,切削液是切削加工过程中的辅助性材料,也是改善加工条件及效果的一个辅助手段,合理使用切削液有助于切削的顺利进行并达到预期的工艺要求,但不应对其抱有超过其功能的不切实际的期望,诸如产品精度、光洁度、刀具寿命等都主要依靠机床结构、加工工艺以及刀具等因素来解决。如果机床本身的精度、刚性不够就不可能加工出高精度的产品。但在机械因素已固定的情况下,合理选用切削液则可获得可能达到的最佳效果。例如超精磨削加工,在改用清洗性、润滑性更好的切削液时,产品光洁度及加工效率都可得到一定程度的提高。如果仅从机械因素加以改进则要困难得多。
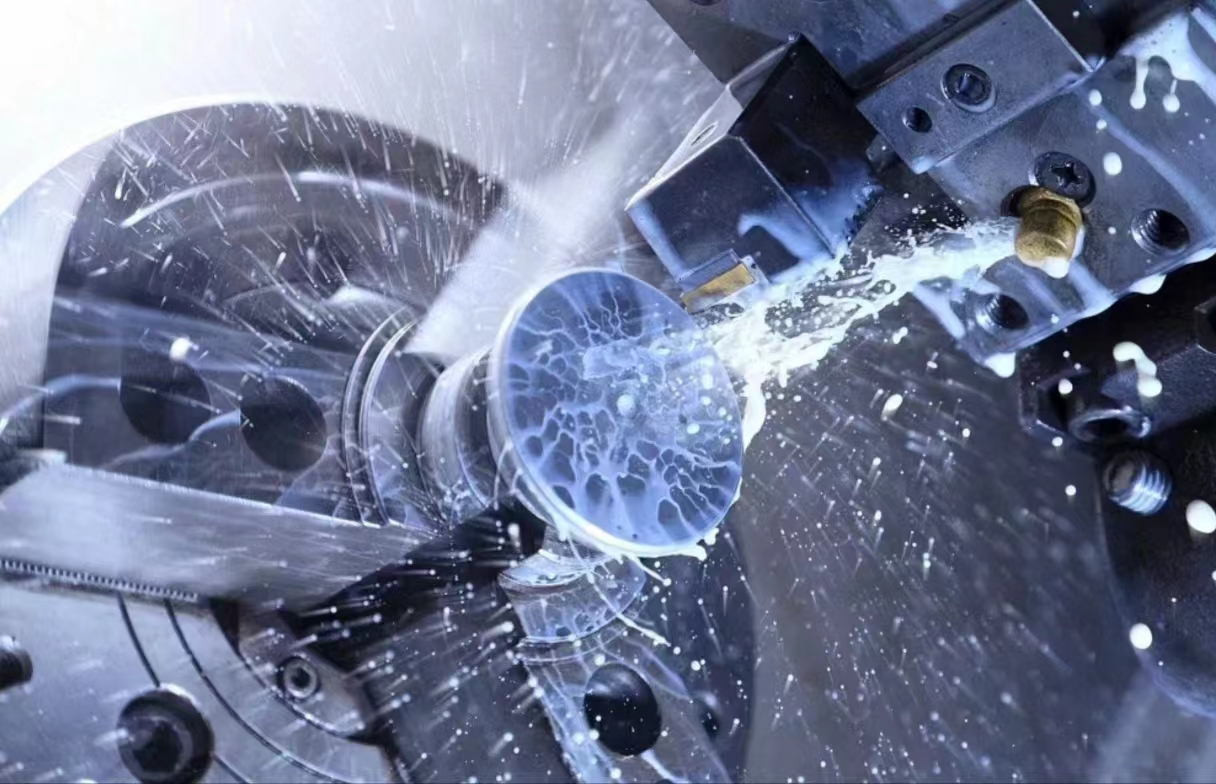
文章和图片均来自网络,本文作为学习参考,感谢作者的辛苦付出,如有不当,请联系客服电话400-856-8088删除。